A neutron strain scanner (NSS) is a neutron diffraction instrument optimised for three-dimensional spatially-resolved determination of bulk residual stress through the measurement of lattice spacings in polycrystalline materials. To accommodate a wide spectrum of experiment and sample types and to meet the required accuracy and precision, NSS are usually equipped with machineries and devices as follows:
- Sample stage. A platform with high-resolution translation and rotation stages to position the sample. In some instruments, the accuracy of the sample stage is up to 10 μm for a 250 kg sample. The stage enables accurate sample manipulation to enable strain mapping within the sample for multiple strain components. Eulerian cradles, extra rotation stages, and/or robotic arms are in some cases available to provide additional degrees of movement.
- Sample environment. Systems which allow the sample to be measured under certain conditions, e.g., high/low temperature, pressure, and/or applied mechanical load. Examples of such systems include specially-designed furnaces, cryostats, vacuum chambers, load-rigs, or a combination of them.
- Beam apertures. A set of optics (collimators and/or slits) that enable tailoring of the beam dimensions and directly controls the size of the gauge volume, i.e., the volume of sample material from which averaged diffraction data (including the lattice spacing info) is acquired. This therefore determines the spatial resolution of the strain map. In some NSS, the size of this GV is variable from 0.2 mm up to many millimetres.
- Sample alignment system. A mechanical (e.g., CMM touch probe) or optical (e.g., laser, theodolite, or telecentric camera) to aid with the initial positioning and alignment of the sample with respect to the reference point (real measurement point).
- Neutron detector system. A system that records the diffracted neutron intensities as a function of angle (2-dimensional PSD in a monochromatic instrument) or time-of-flight (in a TOF instrument).
NSS can be classified by whether it belongs to a continuous or pulsed neutron source. A continuous source generally offers higher flux, therefore allowing faster counting time and/or higher spatial resolution and/or penetration depth, but requires monochromatisation to select an optimum wavelength for single peak analysis of different sample materials. In contrast, a pulsed source allows simultaneous measurement of multiple diffraction peaks through the time-of-flight (TOF) method.
Below are brief description of NSS, which are the current participants of the NQL.
ENGIN-X
World-renowned time-of-flight (TOF) neutron strain scanner located at the ISIS neutron and muon source, Didcot, United Kingdom. Link to the ENGIN-X web page can be found here. The primary features of ENGIN-X are as follows:
- Decoupled methane moderator, ensuring a sharp pulse, with neutron flux at the sample position is in the range of 106 n/cm2/s. Primary flight-path, i.e., the distance from moderator to reference point, of ∼50 m, ensuring high TOF resolution.
- Two sets of disk choppers to shape the incident spectrum, with the full range of the polychromatic beam available from 0.5 – 6 Å, enabling measurement from multiple hkl reflections.
- For GV definition, motorized incident beam slit, 0.3-30 mm in vertical and 0.3-10 mm in horizontal. Radial collimator for diffracted beam, interchangeable with 0.5, 1, 2, 3, and 4 mm gauge-width (FWHM) options.
- Two detector banks fixed at 2θ = ±90° to the incident beam and ∼1.53 m from the instrument reference point, enable measurement of two orthogonal strain directions simultaneously.
- x, y, z, and ω axes, with a range of motion of ±250 mm in x and y, 700 mm in z, and 370° in ω. Maximum sample weight of up to 1 tonne, with movement accuracy of 10 µm/100 mm for a 0.5 tonne sample.
- A pair of theodolites for precise alignment of samples
- Sample environment and load rigs available:
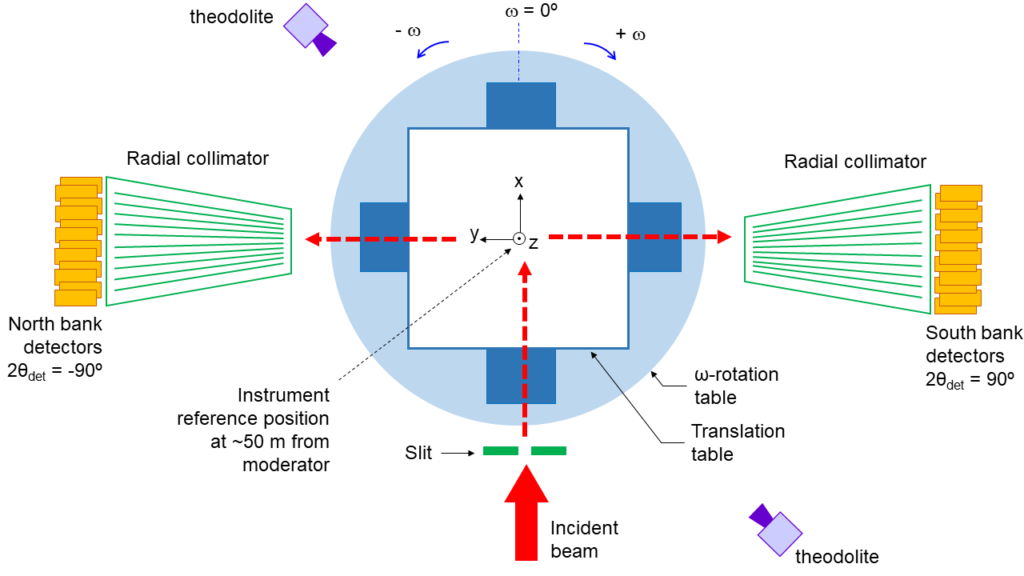
MPISI
MPISI is a monochromatic strain scanner located on the 20 MWthSAFARI-I research reactor, near Pretoria, South Africa. Link to the MPSI web page can be found here. The primary features of MPISI are as follows:
- Double-focusing Si multiwafer monochromator, with wavelength options of 2.53, 1.65, 1.01, and 0.93 Å, . The Si(331) reflection (1.65 Å) is normally used for strain analysis since it provides the reflection of interest in most engineering materials close to diffraction angle 2θ of 90°, hence optimum gauge volume definition. Neutron flux at the sample position is in the order of 106 n/cm2/s
- For GV definition, incident and diffracted beam slits with variable dimension 0.3 – 5 mm in the horizontal and up to 20 mm in the vertical. The diffracted beam slit is interchangeable with radial collimators with FWHM of 1 mm, 2 mm, 5 mm and 10 mm.
- Huber integrated xyz-stage with maximum load of 250 kg and 250 mm travel on all linear stages (movement accuracy ±10 μm for 250 kg sample). A ¼ Eulerian cradle is also available.
- 3He-filled Denex 300TN multiwire area neutron detector with 300 × 300 mm2 active area, providing 2θcoverage of ∼14° at 1150 mm from the sample.
- A pair of theodolites for precise sample alignment.
- Sample environment available:
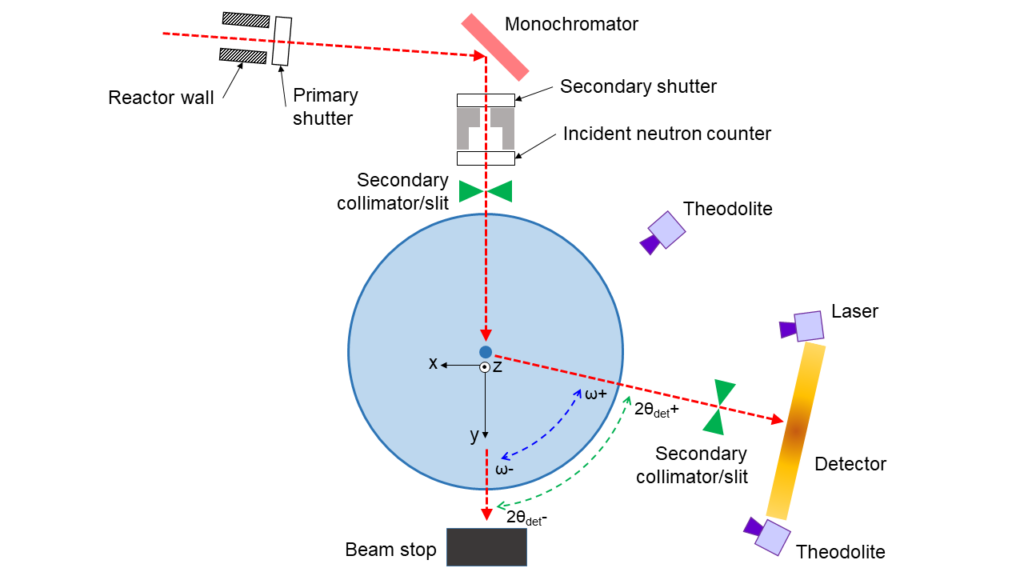
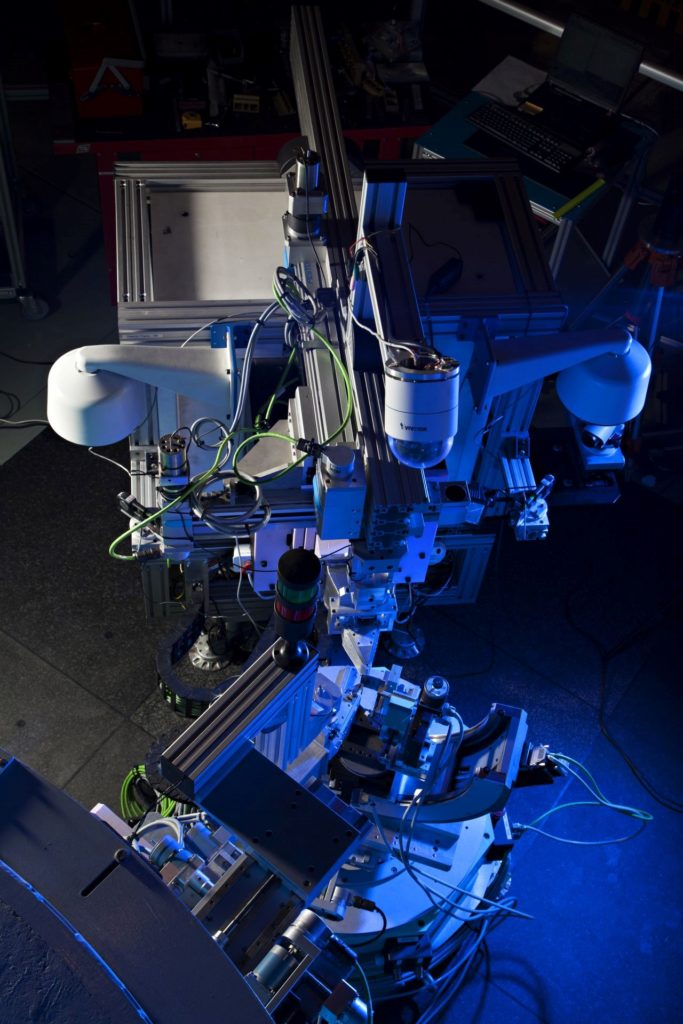
SALSA
SALSA is a monochromatic neutron strain scanner at the continuous reactor source of the Institut Laue-Langevin (ILL) in Grenoble, France. Link to the SALSA web page can be found here. The primary features of SALSA are as follows:
- Installed on a super-mirror neutron guide with relative critical angle of reflection m = 2, therefore delivers high neutron flux with low background. Uses double-focusing type with a column of bent Si perfect crystals provides a wavelength range of 1.3-3 Å, ideal for most engineering metal applications (Fe-, Al-, Ni-, Ti- alloys, etc.). The neutron flux at the sample position is in the range of 107 n/cm2/s.
- For GV definition: suite of radial collimators provide options to respectively define a beam with full-width-at-half-maximum of either 0.6 mm, 2 mm or 4 mm (horizontal and vertical, arranged in series) for both the primary and secondary beam. Automated slit systems available for more flexible GV definition.
- Hexapod sample manipulator: robot with six degrees of freedom achieved by using six independent hydraulically controlled (parallel kinematic) pistons. Enables sample support of over 850 kg, with a range of motion of ±300 mm translation in x and y, 150 mm in z (movement accuracy ±20 μm for > 500 kg sample), and tilt range of ±30°. The hexapod slides on air-pads on a 2.5 m2 delta table, adding 700 mm horizontal translation and 360° omega-rotation. A ¼ Eulerian cradle and a compact rotation stage are also available to mount on top of the hexapod.
- 2-D microstrip position sensitive detector with an active area of 80 × 80 mm2, covering 5° in 2θ
- Telecentric camera system with on-screen measurement features for sample alignment.
- Sample environment available:
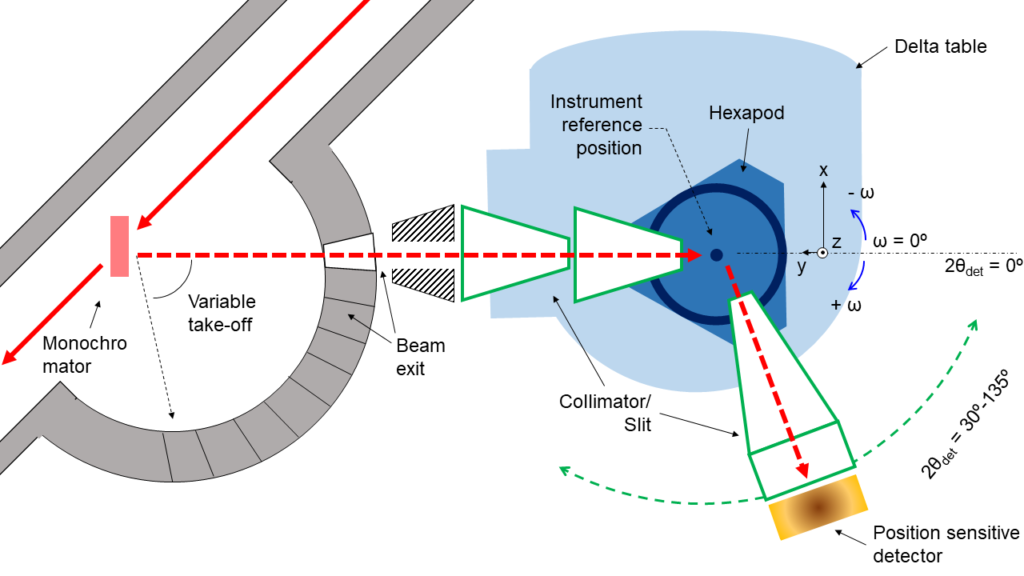
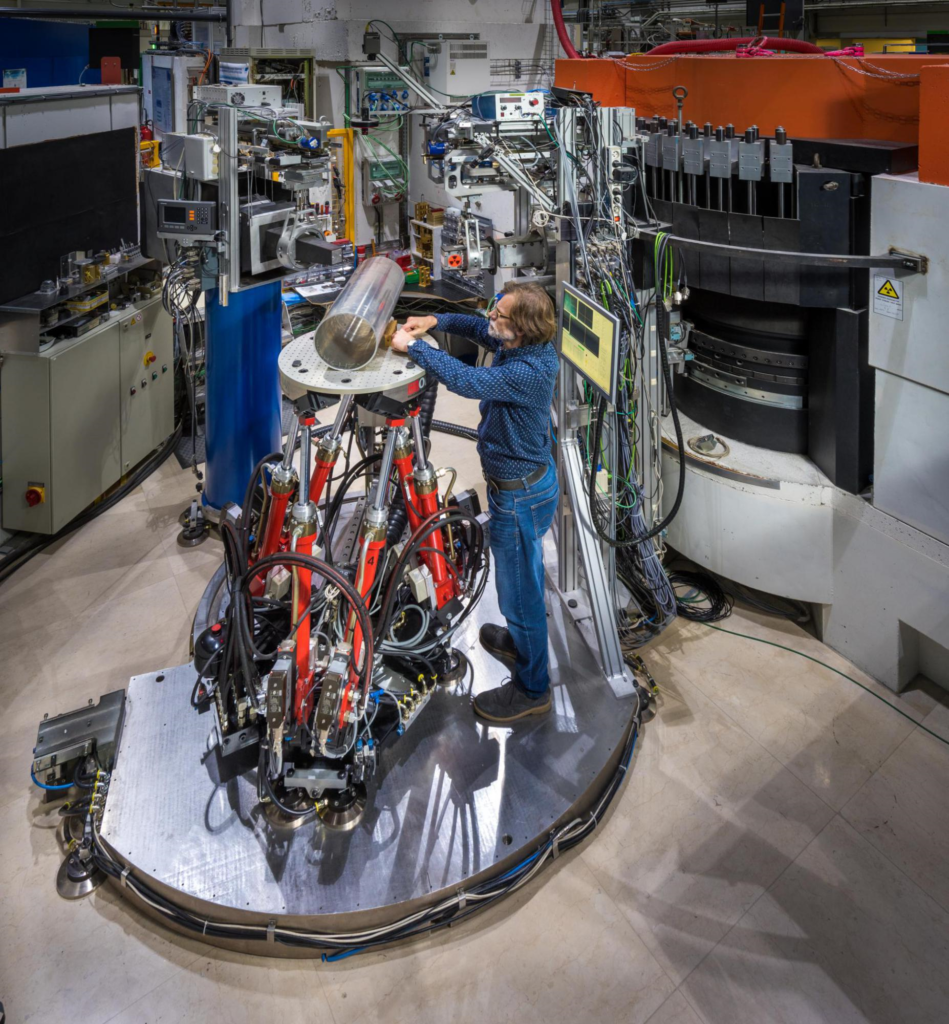
STRESS-SPEC
STRESS-SPEC is a monochromatic neutron diffractometer which offers strain scanning as well as texture analysis capabilities, located at the FRM II reactor in Munich, Germany. Link to the STRESS-SPEC web page can be found here. The primary features of STRESS-SPEC are as follows:
- A flexible monochromator setup using three different monochromators: Ge(511), bent Si(400) and pyrolitic graphite PG(002). Variable take-off angles ranging from 35° to 110° allow optimisation between resolution and intensity for each measurement case. The wavelength range of the incident beam is 1 – 2.4 Å and the neutron flux at the sample position is in the order of 107 n/cm2/s.
- For GV definition: continuously variable slits, up to 7 mm horizontal and 17 mm vertical opening for incident beam and up to 15 mm for the diffracted beam. Radial collimators with FWHM of 0.5 mm, 1 mm, 2 mm, and 5 mm are also available.
- xyz-sample positioning stage with 300 kg capacity, xy-translation of ±125 mm and the z-translation of 300 mm (movement accuracy ±10 μm for 250 kg sample). A full circle Eulerian cradle with a maximum load of 5 kg and ¼ circle Eulerian cradle for heavy samples are also available. Additionally, a positioning system consisting of a Stäubli-6-axes robotic arm (payload up to 30 kg) can be mounted instead of the standard sample stage, which offers more flexibility and allows automatic sample changes.
- 3He position sensitive detector
- Theodolite for precise sample alignment
- Sample environment available:
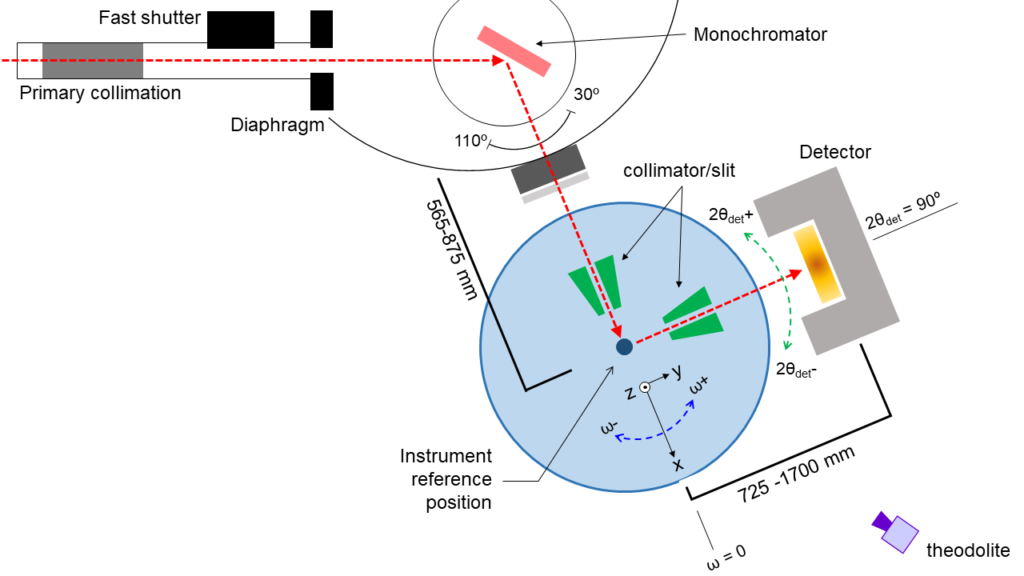
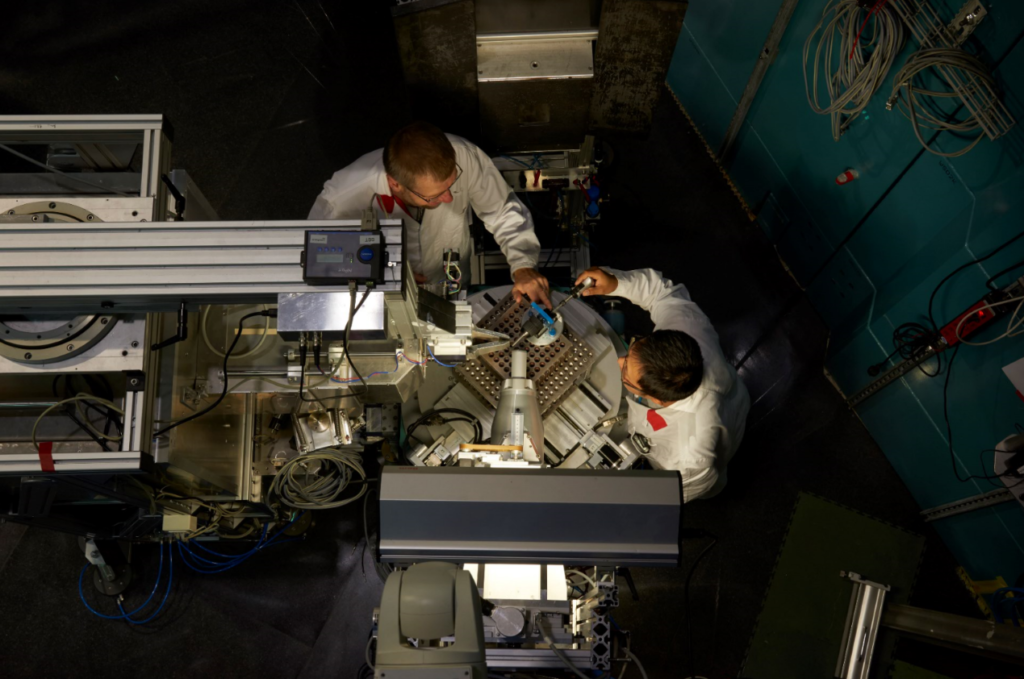