Measurement of residual stresses in different thickness of laser shock peened aluminium alloy samples
This study focused on depth-resolved residual stress results determined with a number of complementary techniques on Laser Shock Peening (LSP) treated aluminium alloy 7075-T651 samples with different thicknesses (6 mm and 1.6 mm). Samples were prepared from a single commercially produced rolled plate that was then treated with LSP. Residual stresses were measured using Laboratory X-ray diffraction, incremental hole drilling, synchrotron XRD (at the 6-BM-A beamline at the Advanced Photon Source) and neutron diffraction at MPISI in South Africa. The LSP treatment resulted in the establishment of compressive residual stresses that varied rapidly in the near surface region. The compressive stresses extended up to 1.5 mm in depth in the 6 mm thick sample. Some surface stress relaxation was observed in the first 25 μm, but substantially large stresses existed at 50 μm.
S.N van Staden, C. Polese, D. Glaser, J.-P. Nobre, A.M. Venter, D. Marais, J. Okasinski, J.-S. Park. Measurement of Residual Stresses in Different Thicknesses of Laser Shock Peened Aluminium Alloy Samples. Materials Research Proceedings 4 (2018) 117-122 (http://dx.doi.org/10.21741/9781945291678-18)
Characterisation of Welding-Induced Residual Stress Using Neutron Diffraction Technique
Pressure vessels comprise critical plant equipment within industrial operations. The fact that the vessel operates under pressure, and may carry toxic, dangerous or hazardous contents, necessitates that care is taken to ensure safety of humans operating it and the environment within which it operates. Residual stress developed during welding of pressure vessel structures can adversely affect fatigue life (mean stress effect) of such structure and lead to corrosion crack growth. This study applies the Neutron Diffraction technique to formulate the stress field distribution of a nozzle-to-shell weld joint of a pressure vessel. A number of experiments are conducted using the Submerged Arc Welding (SAW) process at various parametric combinations to develop a number of specimens with different stress profiles. It is shown that the hoop stresses close to the weld centre line (WCL) are highly tensile and have values close to the yield strength of the material. The ideal parametric combination is also determined based on the results with lowest stresses. The results obtained in this study are congruent to the results of similar studies in literature.
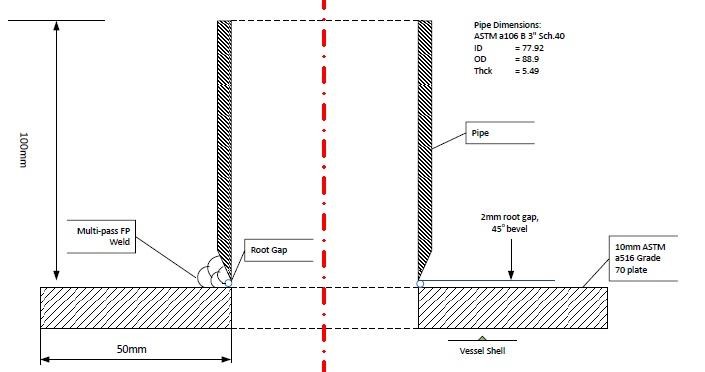
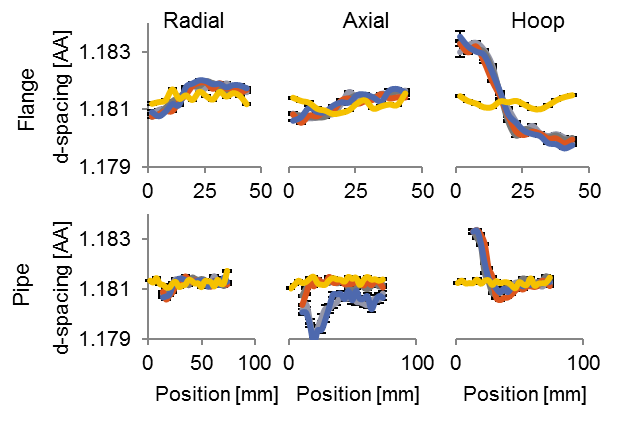
M.C. Zondi, A.M. Venter, D. Marais, C. Bemont. Characterisation of Welding-Induced Residual Stress Using Neutron Diffraction Technique. Journal of Pressure Vessel Technology. 139(6), 061402 (Oct 12, 2017) (http://dx.doi.org/10.1115/1.4037445)
Comparison of residual stress evolution in additive manufactured Ti-structures
One of the major challenges faced by additive manufacturing (AM) is the residual stresses generated during AM part fabrication often leading to unacceptable distortions and degradation of mechanical properties (Figure on the left). Therefore, gaining insight into residual strain/stress distribution is essential for ensuring acceptable quality and performance of high-tech AM parts. Nondestructive neutron diffraction measurements were performed aimed at comparing the residual stress built-up in Ti–6Al–4V AM components with different microstructures produced by Wire+Arc Additive Manufacturing (WAAM) and by laser cladding process (CLAD). It turned out that the stress state in such a thin walled structure can be essentially characterized by a longitudinal component with high tensile stresses near the baseplate and compressive stresses at the top (Figure on the right). CLAD and WAAM processes have been observed to yield similar stress profiles with differences only in normal stresses near the base plate [1, 2].
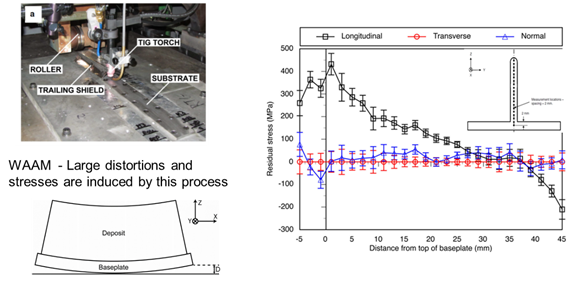
[1] B. Szost, S. Terzi, F. Martina, D. Boisselier, A. Prytuliak, T. Pirling, M. Hofmann, D. J. Jarvis, Mat. & Des. 89 (2016) p559 (http://dx.doi.org/10.1016/j.matdes.2015.09.115)
[2] F. Martina, M. J. Roy, B. A. Szost, S. Terzi, P. A. Colegrove, S. W. Williams, P. J. Withers, J. Meyer, M. Hofmann, Mat. Sci. Tech. 32 (2016) p 1439 (http://dx.doi.org/10.1080/02670836.2016.1142704)
Welding – Non-destructive analysis from surface to bulk
Welding generally introduces substantial residual stress into engineering components due to the highly localized and extreme manner in which heat is applied. The resulting high temperatures and thermal gradients give rise to spatial and temporal variations in thermal expansion and contraction, leading to non-uniform plastic flow of the thermally softened material. Determination of stress profiles in weldments is a classic example of the usage of neutron diffractometers in engineering applications. Neutron diffraction is perfectly suited for that, because it conveniently allows one to probe the residual stresses from the surface into the bulk of a sample nondestructively.
The figure on the right shows the stress profile (open symbols) in an austenitic steel weld made by tungsten inert gas (TIG) welding in course of the TG4 project of the European Network on Neutron Techniques Standardization for Structural Integrity (NeT). To study the effects of post processing the sample was also measured after finish milling (photo sequence on the left). Using a new method to also deconvolute [1] and determine the stress profile close to the surface, the full stress profile after milling could be derived and compared to destructive X-ray diffraction measurements and FEM modeling [2]. Predicting the final residual stress fields is crucial in high safety exigence industrial technological processes such as the ones required in power plants technology.
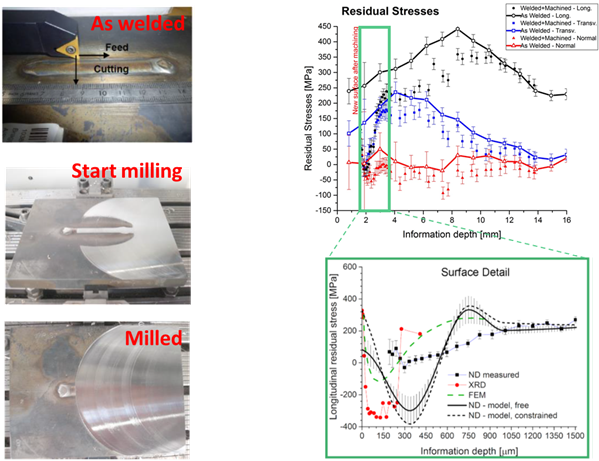
[1] J. Šaroun, J. Rebelo Kornmeier, J. Gibmeier, M. Hofmann, Physica B Cond. Mat. 551 (2018) p468 (http://dx.doi.org/10.1016/j.physb.2018.01.013)
[2] J. Rebelo Kornmeier, M. Hofmann, W. M. Gan, V. Robin, F. Valiorgue, H. Pascal, J. Gibmeier, J. Šaroun, Int. J. Adv. Manuf. Technol. 108 (2020) p635 (https://doi.org/10.1007/s00170-020-05386-8)
Residual Stresses in Metal Matrix Composites
Metal matrix composites (MMCs) are widely used in advanced industries because of their outstanding properties. However, the poor weldability of MMCs is one of the major factors that limit the widespread application of MMCs. Friction stir welding (FSW) is considered to be a promising technique for joining MMCs (Figure top left). As with other welding processes, residual stresses are generated after FSW. Residual stress in the welds is a crucial issue because it significantly affects the weld properties, such as plastic collapse, fatigue properties and stress corrosion, which makes it an essential property that engineers need to assess quantitatively in order to predict the structural integrity of welded components. However, determining residual stresses in MMC welds is quite difficult, due to the quite frequent lack of reliable strain-free reference samples.
Therefore, a new experimental approach to determine the macroscopic and microscopic residual stresses in metal matrix composite welds via neutron diffraction has been developed on friction stir welded 17 vol.% SiC reinforced Al plates as an example material (Figure bottom left). Surprisingly, we found that the profiles of the total residual stress in the reinforcement are entirely different from those in the matrix. The total residual stress profiles in the matrix are dominated by the macroscopic stress, whereas in the reinforcement the elastic mismatch (microscopic) residual stress prevails (Figure at the right, [1]). The results were further used to adapt and qualify a FEM model to predict micro- and macro-stress profiles in FSW compounds [2].
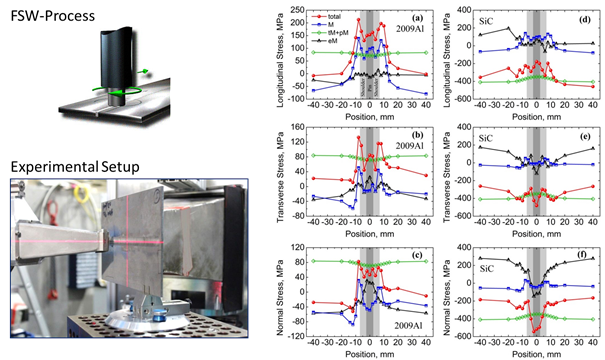
[1] X.X. Zhang, D.R. Ni, B.L. Xiao, H. Andrä , W.M. Gan, M. Hofmann, Z.Y. Ma, Acta Mat. 87 (2015) p161 (http://dx.doi.org/10.1016/j.actamat.2015.01.006)
[2] X.X. Zhang, D.Wang, B.L. Xiao, H. Andrä , W.M. Gan, M. Hofmann, Z.Y. Ma, Mat. & Des. 115 (2017) p364 (http://dx.doi.org/10.1016/j.matdes.2016.11.070)